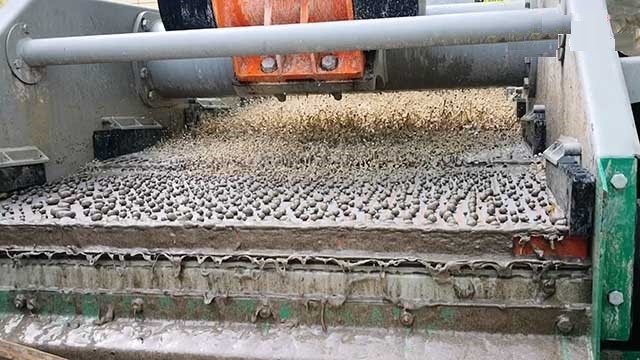
We all know that the Shale Shakers are the first line of defense and the shale shaker screens in it play a very crucial role in the drilling operation. To decide the quality of the Shale Shaker Screens, it is very important to know the Life and Performance of the screens. Longer life definitely gives satisfaction and confidence to drilling operators. This in turn saves money for the operators and improves the efficiency of the rig.
Shale Shaker Screens life
Life of shaker screens is determined by the duration it can last on a shale shaker. The same model/size shaker screens may reflect dramatically different life time when used under different working conditions at site such as the drilling fluid type and properties, the drilling depth, drill solids/cuttings, ambient temperature, flow, flow pattern, and other parameters. Also, the way an operator handles a shaker screen will lead to different screen life as well.
The screen life not only depends on the screen quality and drilling condition but also depends on the quality, design, and maintenance carried out on the Shale Shaker / desilter / desander or mud cleaner.
The bottom cushioning rubber on a shale shaker screen is another such feature affecting the screen’s life. The rubber will peel off soon if it is not properly bound. Finally, shaker screen can be broken swiftly if the vibrations are irregular or the weir strips on the Shaker screen panel are not present. Moreover, shale shaker screens without rubber will lead to a comparatively deteriorated performance.
Performance of Shale Shaker Screens
Besides the life of a Shale Shaker Screen, there are other features that reflect the screen quality such as the filtration efficiency, conductance, use of right mesh/API number etc. High filtration efficiency requires more open area. So, a screen designer should ensure the screen has a maximum non-blanked area. Also, the rate of screening improves as the conductance of screen increases . The conductance data of screens can be tested by professionals under ISO or API standards.
Even the good shaker design adds to the performance of the Shale Shaker Screens. For example, one of the major factor is the design of weir strip or the possum belly mud discharge. This decides both the life and performance of screens as well as the shakers.
How we verify shaker screen life and performance
We must understand the complete working condition of the screen to verify a shaker screens life and performance. Firstly, we must analyze the quality and performance of shale shaker screens under all the possible scenarios discussed above. Many users will refer to an OEM screen or to a replacement screen manufacturer as standard. However, we can easily find differences when we compare the same type of screens from different suppliers under the same operation conditions.
Eg: We can put 3 panels of FLC500 series flat screen replacement on an original shaker. Screens are API 200, working condition is a drilling depth of 3000m and core diameter of 156mm of multiple lateral well. Let’s suppose under such working condition, original Derrick FLC500 series flat screen lasts for 300 hours. The quality of the replacement screen is considered to be good if it lasts for 280~300 hours under the same working conditions. It can be confidently declared as poor quality if it lasts for anything less than 200 hours.
Based on above tips, we can select shaker screens at different prices and get related cost-efficiency.
VPrime team is technically advanced to predict the life of the Shale Shaker Screens and make the consumption analysis by analyzing the conditions of the operations at the site. We have often received positive feedback from our customers who have experienced and shared with us that the life of a VPrime screen is nearly double the life of the screens available in the market. VPrime has also taken the initiative to train and advise the operators on Do’s and Don’ts to increase the life of the screen.
We will come up with the Do’s and Don’ts for increasing the life of the screen in the upcoming blogs. Thank you.