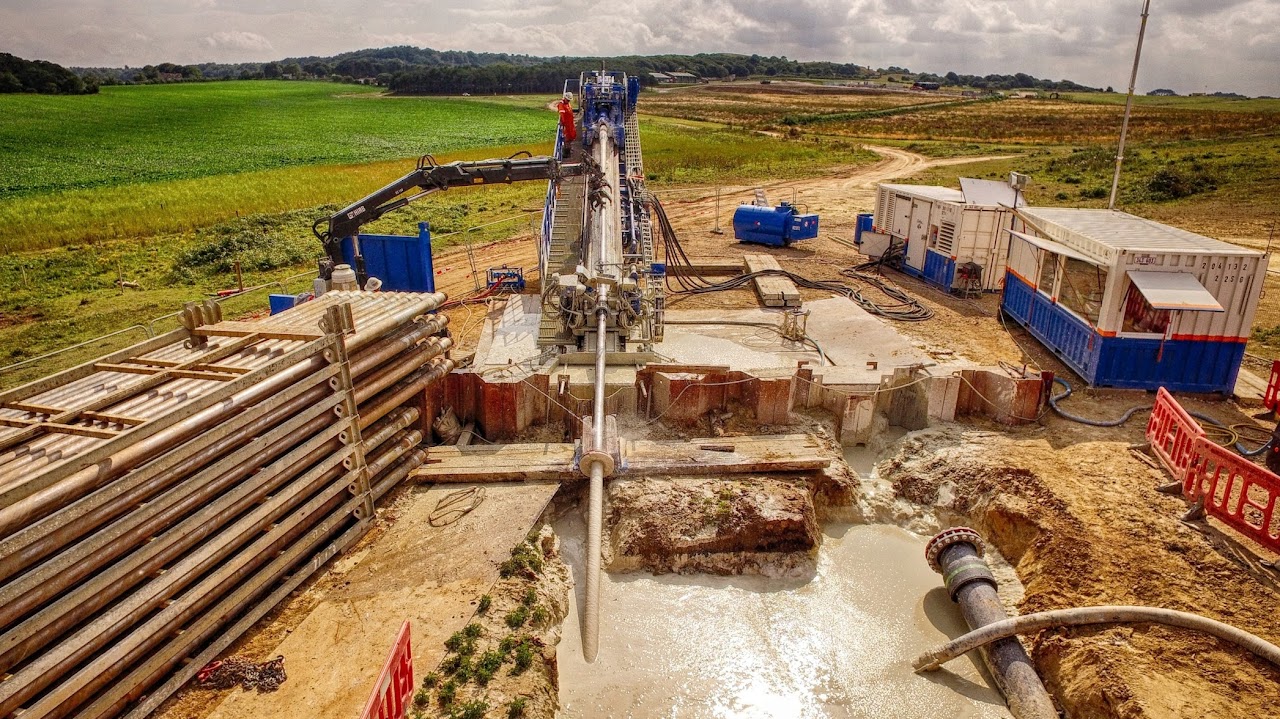
Horizontal directional drilling (HDD) is successful for various reasons, including continuously evolving drilling equipment, tools and as well as more experienced operators using the tools.
When talking to a few drillers, we realize that they have forgotten the importance of the drilling fluids which can make their projects very successful if handled properly. Most successful people plan for their success by using a drilling fluid program to avoid unnecessary and anticipated troubles. Every year drilling fluids companies spend an incredible amount of time and money with training programs devoted specifically to drilling fluids for the drilling industry.
An old saying “It’s just mud” is no more. The industry understands well now. Drilling fluids must perform some basic functions for any mud drilling application to be successful :
- Remove cuttings from the borehole
- Cool and lubricate the tools
- Suspend the cuttings
- Stabilize the borehole
- Control fluid loss to the formation
Properly designed drilling fluids should take care of all the above functions. Measuring certain properties of these fluids allows us to predict how the fluid will perform when pumped into the borehole. We typically monitor make-up (drilling water) water quality, viscosity, fluid loss, gel strength, yield point, sand content, and density of the drilling fluid.
Make-up Water Quality
Let’s start with make-up water quality as it can have the single largest impact on the drilling fluid properties and should not be ignored. A typical HDD fluid will contain approximately 97 percent water and 3 percent additives, thus the importance of water testing. With this in mind, sourcing good water is a must — each and every time. Mud Engineer can test the water and decide the chemicals and prepare the mud program based on the quality of water. If water is too impure, another source of water may be looked for.
Fluid Viscosity
Viscosity by definition is resistance to flow or how thick or thin the fluid is. As the definition indicates the more viscous the drilling fluid is the more resistant to flow it behaves. While a higher viscosity fluid helps carry the cuttings along the bore path, it takes more horsepower to move the thicker fluid and creates more downhole pressure. Depending on the formation and its depth, excessive downhole pressure generally leads to loss of returns or frack outs. Higher viscosity drilling fluids are also much more difficult to clean if a recycling system is being used. Some of the negative effects of higher viscosity can be minimized by careful selection of the drilling fluid additives used to build viscosity.
There are few ways to measure viscosity on the jobsite. The easiest and most common test method is the marsh funnel. Every rig must have a marsh funnel and cup. Learning to use one becomes part of the rig start-up training provided by the drill manufacturer. The second apparatus used for testing viscosity is the direct indicating viscometer. The VG meter — as it is referred to — is a bit more involved to operate and maintain. Unlike the marsh funnel that only measures the viscosity of the fluid, the VG meter will give other readings that allow you to measure AV (apparent viscosity), PV (plastic viscosity), YP (yield point), YP/PV ratio and gel strength. We will use these readings to measure and monitor the performance of the drilling fluid.
Just, what do all these readings tell us and why do we need to know?
As the name implies AV and PV are measurements of viscosity. Yield point is a measurement of the drilling fluids carrying capacity in a dynamic state, or when the fluid is moving along the borehole. Gel strength is a measurement of the carrying capacity of the drilling fluid when the fluid is static or when the fluid is not moving in the borehole. Each of these fluid properties is important to the efficiency of cuttings removal in HDD applications. Gel strength is measured at both 10 seconds and 10 minutes. We monitor both 10 seconds and 10 minutes, as it is important to have the 10-second gel strength high enough to suspend cuttings when the fluid pumping is stopped but not an excessively high 10-minute gel that has to be broken to reestablish flow. Having a 10-minute gel more than two times the 10-second gel is referred to as a “progressive gel.” Remember, the gel strength is a measurement of the fluid in a static condition and these gels must be destroyed to get the fluid moving again. If the gels are too high, the pressure to sheer the gels may be greater than the formation will bear, causing the fluid to flow into the formation rather than back along the borehole. The YP/PV ratio also gives you some valuable information if you are recycling the drilling fluid. The YP/PV ratio will give you an indication of ultra-fine buildup in the drilling fluid indicating when it may be time to dump the fluid and start over.
Controlling Fluid Loss
Controlling fluid loss or filtrate loss — of a fluid is also something very important to a successful HDD drilling. Fluid loss is the willingness of the fluid to give up its liquid phase when put under downhole pressure. Fluid loss should not be confused with the term ‘loss circulation,” which is loss of the drilling fluid in its entirety to the formation not just the liquid phase.
Monitoring and controlling fluid loss provides a predictable thin, low permeability wall cake with excellent lubricity. High fluid loss promotes a thick, tacky wall cake and allows the liquid phase of the drilling fluid to penetrate the formation. Filtrate intrusion into the formation will water wet sands, silts and clays, causing destabilization and swelling. Fluid loss of the drilling fluid is measured on the jobsite with a filter press. The portable filter press allows us to put the drilling fluid under pressure for a period of time to emulate how the fluid will perform in the borehole under normal drilling conditions. The filtrate is captured and measured from the test sample, recording the results in milliliters. The thickness of the filter cake is also examined and measured. A good filter cake should be thin, tuff and slick to touch.
Density & Sand Content
Density and sand content are usually monitored only on sites where a recycling system is being used. Density is measured onsite by the use of a mud balance or mud scale. Measuring both incoming and outgoing fluid densities on a solids control system provides an excellent picture of how well the solids control system is performing; however, the main focus should be toward the outgoing fluid as that is what the borehole will be seeing. Sand content testing on outgoing slurries will also provide valuable data as to when you may need to dispose of the slurry and start over. A good target is 0.25 percent or less sand in the freshly cleaned fluid to protect the pumping system and keep the density low. Maintaining a mud density in the 9-lb/gal range is the goal when using a recycling system on a typical HDD project, but it may not be practical in some situations. Typically, we would recommend discarding a fluid with a density after cleaning 10 lbs/gal or more.
Finishing Thoughts
The drilling fluids industry has evolved with the HDD industry over the past few decades to provide products that are pre-engineered to provide the properties that we realize so important. Second-generation, extended bentonites that hit on the issues of higher viscosity, lower fluid loss, and predictable gel strengths are some examples. We have engineered these products knowing the only testing equipment onsite is probably a marsh funnel allowing the customer to mix to a specified viscosity. With the product mixed to the specified viscosity for the soil type to be drilled, the fluid loss and gels will fall into the desired range, as well. Other additives may be added to further manipulate the final fluid properties with the use of the marsh funnel and a well-calibrated measuring cup.